Sand
The sand industry along with other material processors face mounting costs when their materials, if quarried wet, have to be stockpiled to allow gravity drainage to take place before they are eventually force dried in kilns, or oil-fired furnaces.
SAND
Similarly, whilst the material has been stockpiled, it can become further saturated by the rain if stored outside, or build up a large moisture content through condensation when stored in a hot, or humid environment.
Conscious of the high price of heating oils and further storage costs to partially alleviate such instances, our patented ‘AMR’ system removes such high costs through the drying time of the material being reduced to a matter of hours. This in turn leads to quicker handling and movement. Thus production and sales can continue throughout the year, including the wetter months and ultimately reduce costs considerably.
If saturation levels of your product is not the problem, for instance in a dry or hot climate, you may require the water from within the material. In such a case our water-recirculation system will draw the water from the product and produce a clear solution that will enable you to recycle the water and reduce the need to transport water to the site.
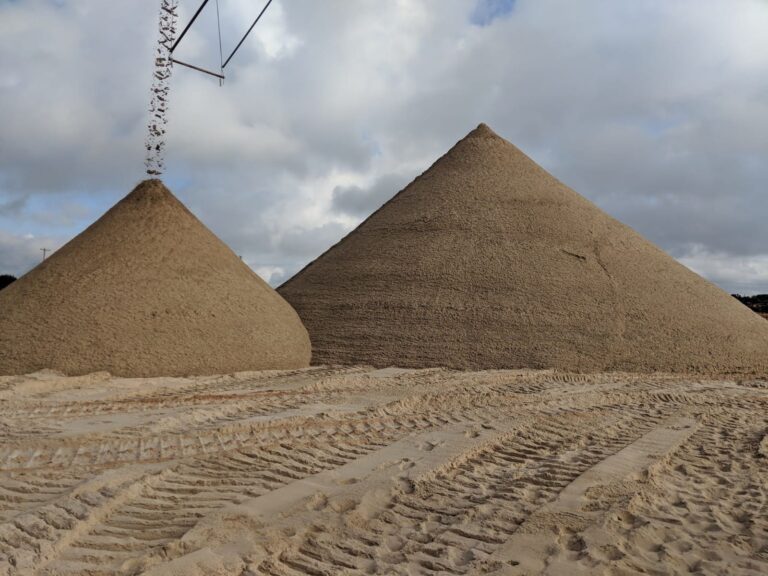
Situation
The customer that operates multiple sites was conscious of the constant high operational cost of wet material requiring increased amounts of gas in the forced drying of the 100mesh material. Added to this was the high price of finding and drilling bore holes for new water to be used in the sand washing process. The customer contacted Moisture Reduction Systems to provide a solution that will eliminate the high moisture in their material and deliver a subsequent cost reduction in the drying plant and water supply chain.
The average moisture level of the material was 14.00% moisture content with a typical natural drainage time to approximately 6.00% of up to 5 days.
The challenge
- Reduce moisture content to create significant cost reduction in the drying process
- Provide water recycling aspect to the water removal process
- Efficient and reliable operational use
- Commercial viable and short time frame installation
- Material sizing was 100 mesh
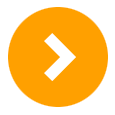
Solution
Moisture Reduction Systems drew upon their significant knowledge and experience of the operational process and requirements at sand plants in order to design and install a bespoke- tailored solution that would deliver to the fast acting solution that was required. The system was installed to match exactly the stockpile footprint with individual sections installed so as to allow moisture reduction of the material to begin as soon as material had been placed on the large 270-degree radial arm area. Similarly, upon reclaiming of the material, the system could continue to operate on individual sections without compromising the yet to be reclaimed material. The result was that the system delivered a final moisture level of 3% moisture content and in some instances 2.7% after 24 hours. This was in stark contrast to the previous 5 days to achieve 6.0%. Furthermore, the system recycled the removed water from the stockpile back into the wash plant at an average rate of 600 gallons per minute and 164m3 per hour. The customer ordered and implemented the system across its two other sites covering a total of 9 stockpiles.